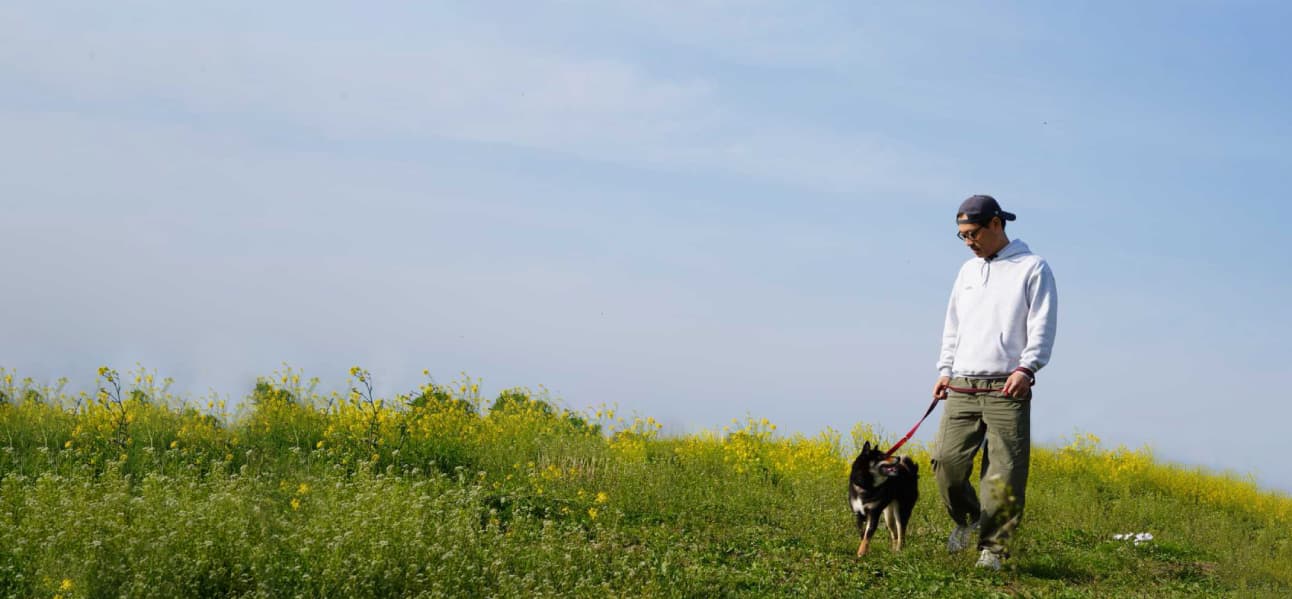
問いをつくれ。
社長ブログ
卒制報告_最終回
2020-03-11(卒制報告_19のつづき)
本日、搬出日。
10時に展示会場に到着すると、
同じ学科で撤収作業をしている学生は一人もいません。※ムサビ正門。学内立ち入り禁止で人がいません。 というのも、
中止になった学校主催のパーティの代わりに、
今夜、国分寺で打ち上げが予定されていて、
午後遅めの時間帯に作業して、
そのまま打ち上げに行く段取りの人がほとんどだから。残念ながら、私はそこには合流できず。
ムサビから搬出した後、
今度は作品を搬入する必要があるからです。搬入先はどこかといえば、公募ガイド社のオフィス!
こんな大きな作品を置く場所は自宅にはなく、
かといって解体して眠らせておくのももったいないので、
なかば事後報告的に他のメンバーからの承諾を得て(ゴメン
置かせてもらえることになったのです。
※モナリザ。不定期に変えていこうと思います。それにしても、打ち上げ…
今頃、さぞかし盛り上がってるんだろうな。
改めて謝恩会もあるらしいけど、
撤収後のこのタイミングだからこその解放感、
共有したかった。卒業式もなくなったし、
何とも締らない終わりになってしまいました。※卒制報告は今回でおしまいです。20回ものお付き合い、ありがとうございました。
卒制報告_19
2020-03-09(卒制報告_18のつづき)
2月29日の設営日に続き、3月1日は講評会がありました。
設営日に展示会と卒業式が中止になる旨の通知があったことは、
以前のブログで書いた通り。講評会では、
デザイン情報学科に関係する先生約20名を前に、
制作者がプレゼンを行い、先生方からの講評を経て、
その後の審査会で評価が付けられます。約20名の先生は、
過去に何らかの授業でお世話になった方が大半。<良い点>
・簡単な装置なのに描画できる範囲が広い
・宙に浮かんで見える朔望が造形物として魅力的で、この先の展開も面白そう
・子供というより大人向けで、オブジェとして企業のエントランスとかに置いたら?
<改善点>
・この展示方法だと(後ろの情報に邪魔されて)モナリザを認識しにくい
・「朔望」というタイトルと作品の中身はちょっと違うかもねまとめるとこんな感じの講評でしたが、
ちょっと嬉しかった?のが、「以前の講義での作品はどこか会社員的な作風だったのに、
ずいぶん雰囲気が変わりましたね」という意見。
何人かの先生から同じようなことを言われ、
あとスタッフとしてお手伝いいただいている通学の美大生からも、
「何やっておられる方ですか?」
と聞かれたりで、
やっぱり数年で変わったんだろうか?と思う。ちなみに、例年は先生(+学生たちが横で傍聴)に対し、
プレゼンと講評を1度で行うらしいのですが、
新型コロナ対策ということで、
4~5名1組を対象に計4回のプレゼンを行うスタイルに。なのでいつ回ってくるかよくわからない先生方を、
自分の作品近くで待たなければならず、
他の人のプレゼンや講評を聴くことができませんでした。個別の作品については、
すき間の時間で見て回ったり、個別に話を聞いたりしたけれど、
みんなのプレゼンや先生方の講評も聞きたかった。結局、時間もほぼ丸一日かかったし、
コロナ対策としても、講評会としても、
このやり方はよかったんでしょうかと疑問に思う。卒制報告_18
2020-03-06(卒制報告_17のつづき)
2月第3週。
作品本体の提出も終わり、
残すは展示細部のブラッシュアップのみ。人によっては、
いったん仮作品で受付だけ乗り切り、
残り2週間で作品本体を仕上げていくケースもあるみたいですが、
私の場合、作品は出来上がっているので、
設営日までの残された時間で説明パネルの精度を上げていきます。あっ、そうだ!
作品タイトルを書くのを忘れてました。タイトルは『朔望 sakubou』
朔望とは月の満ち欠けのことです。ひとつひとつの木球が月の満ち欠けに見えること。
その木球をディスプレイの画素に見立てて、自在に描画できる装置。が作品コンセプトです。
だから、コンセプトパネルの方向性としては、
「この装置でこんな描画も作れます!」を見せていくべきと考え、
〇を白黒に塗りつぶして描ける絵を探ってみることにしました。単に白黒2階調ではなく、
斜め線やグレートーンも表現できます。
だから、モナリザや花札なども表現できて、
やっているうちにこっちの方が楽しくなってしまった(笑もっと初期段階でこの試作を数多く作っていたら、
作品の方向性も変わっていたかもしれないな、
と作品提出した今、改めて思ったり。
やはりデザインは”試作がすべて”ということなのです。卒制報告_17
2020-03-05(卒制報告_16のつづき)
2月16日(日)。
いよいよ、提出締切日。
今日までに受付を完了しないと、卒業の資格を失ってしまいます。搬入をお願いしている会社さんとは、
鷹の台キャンパスの正門に13時に待ち合わせ。
2tトラックを迎えに行ったら、
組み立てを担当してくれたお2人+1名の3人で来てくれてました。朝から降っていた雨も小平地域ではあがっていて、
なんとか濡れずに搬入できそう。1台50kgくらいもあり、
かつ繊細なパーツで構成されている大型の作品ということもあって、
搬入は本当に大変です。3人+私の息を合わせながら、
9号館B1の展示会場まで慎重に運び込み、
安全のためのベースを取り付けるなど、最後の組み立てを完了し、
何とか受付を済ませることができました。それにしても、こちらの会社さん、仕事が本当に丁寧。
美術系の学校を卒業したスタッフさんが多いということもあって、
造形物の取扱いに慣れているし、
何より作り手の気持ちをがわかっている。「ここ、丁寧にやって欲しいな」と思うところは、
言わなくても細心の注意を払ってやってくれるし、
むしろ先回りしていろいろな気配りをしてくれる。
ただの鉄工屋さんや運送屋さんなら、
こんなに何事もなく進んだかどうか。
お願いして本当に良かった。卒制報告_16
2020-03-04(卒制報告_15のつづき)
2月第2週(提出締切りの週)。
フレーム製作と最終組み立てをお願いしている会社さんから、
「組み立てのスケジュールが確定したのですが、立ち会われますか」
と連絡が入る。「ちょっと時間がないのでお任せします」
という回答をするはずもなく、
指定された日時に工房を訪れると、
ちょうどアクリル板に木球を仕込む作業中でした。当然、私も途中から参戦。
いよいよ最終形に近づいているという現実感と、
イメージ通りできあがるのかというドキドキ感。※担当してくださったお2人はともに美術系の学校卒でした。 担当のお二人の丁寧かつ出際のよい作業のもと、
組み立てはどんどん進み、
4時間くらいでついに完成!1号機 2号機(逆光にて) 心配された木球の回り具合ですが、
完ぺきではないものの、
コンセプトに支障ない程度には回ってくれています。今週末の提出締切りに間に合う目途が立ち、
とりあえず、一安心です。東京マラソンをみて
3/1(日)の東京マラソン。
卒制の講評会があったので、リアルタイムでは視聴できず。
録画を見るまで結果を知りたくなかったので、
帰りの電車内の動画ニュースから目をそらし、
スマホも封印で帰宅しました。結果、大迫選手の激走、見ごたえがありました。
22km過ぎで遅れはじめた時は、
「キツイかな」と思いましたが、その後のレース展開が見事。サブスリーレベルで4分/㎞くらいのペースなのですが、
それでも3秒/㎞違うと体感的にかなり違うので、
3分/㎞ペースだと1~2秒のラップ差がものすごく速く感じているはず。
そのあたりのレースマネジメントがうまかったですね。ただそれだと自分との戦いなので、
他人との競争には勝てない。
そういう意味で井上選手のチャレンジも素晴らしかった。レース独特のあの感じ、また味わいたくなりました。
それには練習に向かう勇気が必要ですが。卒制報告_15_突然に終わりを迎えた卒業制作
2020-03-02(卒制報告_14の続き)の予定でしたが、
ちょっと内容変更して書きます。2月29日(土)、
鷹の台キャンパスで設営作業。
作品本体のブラッシュアップは当然のことながら、
展示パネルをセットしたり、
バナーやプロジェクターをワイヤーで吊ったり、
展示物としての完成を目指す。午後になってアナウンスがあり、
特に構えることもなく集合場所に行くと、
1枚の紙が配られ、課程長から以下のコメント。「卒業展示および卒業式は中止します」
まじか…
都内の美術系の学校は例外なく卒展を見送っているらしい。状況考えると当然の流れだけど、
311の時もムサビ卒展は開催したと聞いていたので、
どこか高をくくっていたところがありました。
でもまあ、そりゃそうですよね…これまでゴールとして目指してきた卒業展示と卒業式の両方がなくなった今、
駆け抜けるべきは明日(3/1)の講評会と3/6以降の作品撮影。もともと「人に見てもらうことこそモチベーション」というタイプでもなく、
自分が納得できるかどうかでやってきたので、
ここへきて手を抜くとかありえないですが、
正直、内心は複雑です…
※講評会が終わったらみんなに配ろうと思っていた案内状。
日の目を見る機会はなくなりました。卒制報告_14
2020-02-27(卒制報告_13のつづき)
2月第1週。
アクリル板の加工が始まったということで、
現物を確認しに工場を訪れる。現場に通され、
「こちらです」と先行して加工された2枚のブツを見せられる。
※2枚重なっています。持参した木球を2枚のアクリルに挟み込み、
回り具合をテストしてみましたが、
アクリルをカバーする剝離紙が貼ってあるのと、
2枚をきっちり密着させた状態ではないので、
いまひとつ回りが悪く、不安になる。担当の鈴木さんは、
「さっき社内の人間で試してみたら、きちんと回ってましたよ」
と言ってくれたものの、
自分の目で確認しないことにはそんなの信じられない。とは言うものの、この期におよんで打てる策もなく、
このまま残りの2枚も進めてもらうしか、
実質的な選択肢はない状況。翌日、フレーム製作と最終組み立てをお願いしている会社に持ち込んでもらうことになっていたので、
自宅で加工した木球たちも一緒に配送してもらえるようお願いし、
その日は帰りました。
※加工済みの木球。一球ずつ丁寧に紙にくるみました。この状況においては、
自分が頑張って何とかできることはほとんどなく、
神様にお祈りするくらいしかできない。
やれるものなら、徹夜でも何でもして、
納得いくまで出し尽くすのに。作品提出まで10日を切り、不安しかありません。
卒制報告_13
2020-02-26(卒制報告_12のつづき)
1月下旬。
アクリル板の加工順を待つ間に、
板に打つネジの位置とフレームの仕様を確定する。こうやって画像を上げると、
仕様は順調に固まっていったように見えますが、
アクリルもフレームも、
職人さんとの間で喧々囂々がありました。アクリルに打つネジの数と位置、
フレームの形状、太さ、塗装などなど、
造形的にこだわりたい私と、
確実に納品まで持っていきたい現場とのせめぎ合い。ときに険悪な雰囲気になりつつ(汗、
何とか着地することができました。今回、学んだこととしては、
木球もアクリルも鉄もそうだったのですが、
世の中の部材には基本的に規格サイズというものがあって、
それをうまく使って設計するのが一番安価で仕上がりもキレイということ。
(それをしてないから、1,000万円の見積りが出てきてしまう)例えば、鉄は裁断や溶接で熱が加わるとどうしても歪みが発生してしまう(+加工賃も発生する)ということから、
職人さんのアドバイスで、
角パイプや鉄板など、できる限り既製サイズをそのまま使う設計で進めました。こういうリアルな現場情報のもと、
「あーでもない、こーでもない」と、
職人さんとプロダクトを作り上げていくプロセス。
仕事にできたら最高やな。卒制報告_12
2020-02-21(卒制報告_11のつづき)
1月下旬。木球が届く。
横10個×縦16個×2セットで320個が必要。
不良品や仕損じの発生も予想されるので、
少し余裕をみて350個発注しました。ここから木工用ステインで半球を塗装していくのですが、
塗装作業については、
イメージ編集Ⅱで制作したSaku-ballで経験済み。いきなり塗ると、
きれいに塗れないし効率も悪いので、1)自作の治具を使って鉛筆で薄く”赤道”を引く
2)鉛筆の線を目印にマスキングテープで非塗装部分を保護
3)水性ステインで塗装という工程をふみます。
塗装は何回重ね塗りするかで色味が変わってくるので、
1~4回の塗りテストの結果、
基本は2回、余裕があったら3回ということにしました。
※右から重ね塗り回数1→4回300個以上あるので、1)も2)も3)もそれなりに時間がかかる。
家族総出で手伝ってもらい、
1週間以上かかって何とか全部塗り終えました。
※これで半分くらいです。それにしても、
工数仕事って人工の力がすごい。
ひとりだと丸一日、10時間以上かかる作業も、
4人でやればさくっと午前中で終わってしまう。本当にいろんな人に助けてもらいながら進んでおります。